In order to turn the thyristor from off to on, it must have certain external conditions, that is, the thyristor anode is applied with a forward voltage and a positive control signal is applied to the gate. When the thyristor is turned on, the control signal does not work. Until the power supply crosses zero, its anode current is less than the holding current, and the thyristor turns itself off.
Since the gate is out of control after the thyristor is turned on, the control of the thyristor actually provides a threshold control with a certain width to trigger the thyristor to turn it on. The gate control circuit is often referred to as a trigger circuit.
The basic requirements for the thyristor trigger circuit are:
1. The trigger signal can be AC, DC or pulse t. The trigger signal can only be active when the gate is extremely positive and the cathode is negative. In order to reduce the loss of the gate, the trigger signal is often in the form of a pulse. The common trigger signal waveform is as shown in the figure.
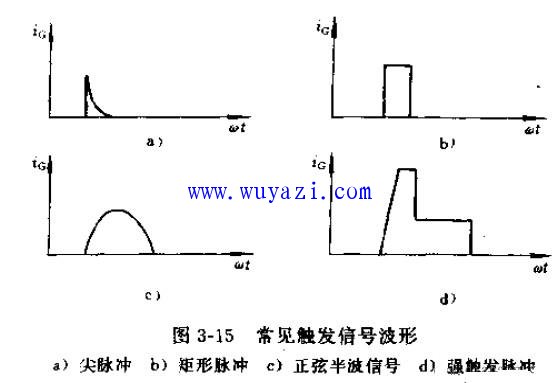
2. The trigger pulse should have sufficient power. The trigger voltage and trigger current should be greater than the gate trigger voltage and gate trigger current of the thyristor. Because the characteristics of the thyristor have large dispersion, and the characteristics vary with temperature, when designing the trigger circuit, the power of the trigger signal should be left to ensure reliable triggering of the transistor, and of course, the signal can not exceed the gate. Extreme limit parameter values ​​(general VCm<10V, IGM<10A).
3. The phase shift range of the trigger pulse should meet the requirements of the converter device. The phase shift range of the trigger pulse is related to the main circuit type, the load nature and the use of the converter device. For example, a three-phase half-wave rectification circuit requires a phase shift range of 150° in the case of an electric nozzle load; Fully controlled rectifier circuit, the phase shift range of the resistive load is 120°. If the three-phase full control bridge works in the rectification or inverter state and supplies power to the inductor, the phase shift range is required to be 0~180°. In practical application In order to normal operation of the device, there are sometimes restrictions on αmin and βmin, so the actual range is less than 180°.
4. The width and steepness of the trigger pulse. The width of the trigger pulse should generally ensure that the thyristor anode current can reach the holding current before the pulse disappears, so that the thyristor can remain in the on state, which is the minimum allowable width. The pulse width is also related to the nature of the load and the main circuit type. For example, for a single-phase rectification circuit, the pulse width is required to be greater than 10 μs for resistive loads and greater than 100 μs for inductive loads. For the dry three-phase full-control bridge circuit, the pulse width should be 60°~120° with single pulse triggering. The pulse width of the double pulse can be about 10°. The steeper the steepness of the leading edge of the trigger pulse, the more favorable the simultaneous triggering of the parallel or series thyristor. Generally, the leading edge of the trigger pulse is steeper than lOV/us or 800mA/us.
5. The trigger pulse must be synchronized with the main loop supply voltage. In order to enable the thyristor to repeatedly trigger on the same phase every cycle, to ensure the quality and reliability of the converter, the trigger pulse must maintain a certain fixed phase relationship with the main circuit supply voltage. The method in which the god trigger pulse maintains a fixed phase relationship with the main loop power source is called synchronization.
A slip ring is an electromechanical device that allows electricity and data to pass through a rotating assembly. A mercury slip ring uses liquid mercury as the electrically conductive element inside the rotating assembly, as opposed to traditional carbon brushes. Mercury is a better conductor of electricity than carbon, and it also has a very low contact resistance. This makes it an ideal choice for applications that require high-speed data transmission or where reliability is critical. Mercury slip rings are used in a variety of industries, including medical technology, aerospace, and defense.
Why do we choose a mercury slip ring?
A slip ring is an electromechanical device that allows electrical current to pass between rotating objects. Slip rings are often used in applications where a cable or connector would otherwise twist and tangle as the object rotates. There are many different types of slip rings, but one of the most common is the mercury slip ring. Mercury slip rings offer several advantages over other types of slip rings, including high reliability, low maintenance, and long life. Here are three reasons why we choose a mercury slip ring:
1. Reliability: Mercury is an extremely reliable material, and mercury slip rings are among the most reliable types of slip rings available. Mercury has a very low failure rate, and it is not affected by changes in temperature or humidity. This makes mercury slip rings ideal for critical applications where reliability is essential.
2. Low Maintenance: Mercury slip rings require very little maintenance. Because mercury is a very inert substance, it does not corrode or generate any corrosive gases that would affect its reliability. Mercury slip rings do not require any lubrication, and they can operate in a wide range of temperatures and environments.
3. Economical Mercury slip rings have a lifetime cost advantage over other types of slip rings as well. Generally speaking, mercury slip rings are approximately 25% more expensive per kilowatt than other types of slip rings. However, because they require less maintenance and have a greater degree of reliability than other types of slip rings, they will save you money over the lifetime of your equipment.
Mercury Slip Ring,Slip Ring Gigabit Ethernet,Slip Ring 400V,Slip Ring Pneumatic
Dongguan Oubaibo Technology Co., Ltd. , https://www.sliprob.com