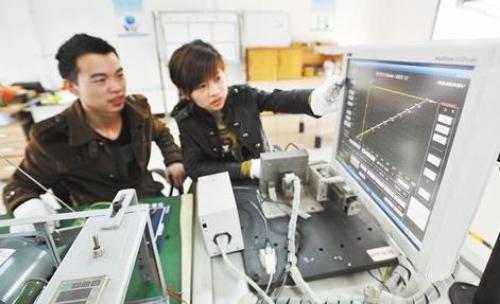
In recent years, the photovoltaic industry has developed rapidly, and the role it plays in power supply has become increasingly prominent. More and more distributed photovoltaic power generation systems are connected to distribution networks, presenting new challenges to traditional distribution networks. The higher requirements for photovoltaic power generation technology and the output of high quality current before grid connection can ensure that the adverse effects of photovoltaic power supply on the distribution network are minimized.
The influence of photovoltaic power on the distribution network mainly includes: increasing the voltage of the access point, causing voltage fluctuations, injecting current harmonics and DC components, DC ground faults, abnormal islands, etc.
This article mainly describes the causes, hazards, and how to effectively suppress the amount of DC injection.
First, the cause of the DC component
The most fundamental reason for the generation of DC components is that the high-frequency SPWM waves output by the inverter contain a certain amount of DC components. The reason that the inverter output pulse width modulation wave contains the DC component can be summed up in the following points:
(1) A given sinusoidal signal wave contains a direct current component
This happens mostly in analog controlled inverters. The sine wave reference signal is generated by an analog device. Because of the differences in the characteristics of the components used, a given sine wave signal itself contains a small amount of direct current. With closed-loop waveform feedback control, the output current waveform and the given waveform are basically the same, resulting in a certain degree of DC component in the output AC current.
(2) DC component caused by pulse distribution and dead zone formation circuit
The SPWM signal generated by the control system must be divided into phases by a pulse distribution and dead-time forming circuit, set a dead zone, and then driven by the drive circuit to isolate and amplify the switch tube. The dispersion of the component parameters will cause the dead-time to be different, that is, the loss in the conduction time of each tube is inconsistent, so that the inverter output contains a DC component.
(3) Inconsistent switch characteristics
Even if the pulse width modulation wave generated by the control circuit is completely symmetrical, due to the differences in the characteristics of the power switch tube in the main circuit, such as different saturation voltage drop during turn-on and inconsistent storage time during turn-off, these will cause the output SPWM wave to be positive and negative. The asymmetry causes the output current to contain a DC component.
(4) DC component caused by the zero drift of the feedback channel of the control system
1) Zero drift of the detection element: Inverter introduces output feedback control, it is inevitable to use various detection elements, the most commonly used is voltage and current Hall sensors. These sensors generally have zero point and temperature drift. Due to the existence of these drifts, the output current contains DC components.
2) Zero drift of A/D converter: In the fully digitally controlled inverter, the output current detected by the detection element needs to be converted into a digital quantity by the A/D converter and pressed by the processor. The control law is calculated. Like the detection element, the A/D converter also has a zero drift, which also causes the output AC current to contain a DC component.
Second, the harm of DC components
The DC component mainly affects the transformer in the distribution network, the current leakage circuit breaker, the current transformer, and the meter. Since these devices all have magnetic cores, the presence of DC components can easily cause magnetic circuit saturation, causing current-type leakage circuit breakers to malfunction, transformers or transformers to saturate, generate heat, generate harmonics, and generate noise, which can lead to operational failure of the entire system. Even embarrassing.
The suppression of direct current injection is one of the key issues for photovoltaic grid-connected networks. IEEE Std. 929-2000 states that the DC component of the photovoltaic system's grid-connected current must be less than 0.5% of the system's rated current. The U.S. regulation does not exceed the current rating of each phase. The value of 0.5%, the national standard GB/Z19964-2005 "photovoltaic power plant access power system technical regulations," the provisions of the DC component should not exceed 1% of its AC rating, at the same time "500kW photovoltaic power generation grid-connected inverter technical specifications" The required DC current should not exceed 0.5% of the inverter output current rating.
Third, the suppression of DC components
The suppression of DC components can be achieved through reasonable design parameter matching. Using isolation transformers before grid connection is an effective way to suppress DC components.
However, over the past decade or so, due to technological advances and cost pressures, the removal of isolation transformers can bring higher efficiency and reduce production costs, and photovoltaic power inverters without isolation transformers are increasingly used.
For systems without an isolation transformer, PV-power inverters that typically use pulse-width modulation (PWM) technology can suppress the DC component output.
The use of a reasonable detection element can also effectively reduce the DC component.
Fourth, the detection of DC components
The detection of DC component generally selects the closed-loop current sensor. The closed-loop current sensor has the characteristics of high precision and small linear error due to small external interference. For the detection of DC components different from the general current detection, the amplitude of the DC components superimposed on the AC signal is very small, and the requirements for the sensor will be even higher.
Current sensors generally have zero error and temperature drift linear error. These errors will affect the DC component. Some of them can be designed by the circuit and software algorithms, while others are not avoided. Choosing the right sensor and using the sensor reasonably can effectively reduce the influence of the current sensor on the direct injection component.
Here we use CASR50-NP as an example to analyze the extent to which these errors affect the DC component and how to eliminate and reduce the effect. The CASR series is a low-temperature drift, small-size sensor developed by LEM for photovoltaic applications. It has four specifications of 6A, 15A, 25A and 50A.
Linear error εl: ± 0.1%, zero offset value Vout: 2.5 ± 0.05, zero temperature drift TCVout: ± 0.7ppm/K, gain temperature drift TCV: max ± 40ppm/K.
The influence of these parameters on the DC component in distributed grid-connected PV inverters will be analyzed.
Linearity error: Since the effective current to be measured is an AC signal, the hysteresis curve in the magnetic circuit is a symmetric curve. The linear error generated in the positive and negative half cycles is also symmetrical. For the DC component, it can be mutual. Offset, so the size of the linear error will not affect the amount of injection of the DC component. The hysteresis curve is shown in the figure below.
Zero drift value: Since the zero offset value of the sensor is a fixed value, in the photovoltaic power system, the zero offset value can be corrected or removed by software to eliminate the influence on the DC injection amount.
Temperature drift: This parameter changes with temperature and cannot be avoided. It directly affects the amount of direct current injection and must be considered in the photovoltaic grid-connected system.
Since the detected signal contains both AC and DC signals, the sensor's integrated error only affects the AC and the DC amount is obtained through integration. These errors will be canceled in the positive and negative half weeks. The above error analysis is combined and the CASR output signal affects DC injection. The amount of parameters is mainly temperature drift error.
With a grid-connected current of 30 Arms, the CASR50-NP sensor detects the grid-connected current. The error at 850C that affects the DC component is:
Total error = TCV_OUT + TCG = 0.12% + 0.24% = 0.36% This error is much better than the 0.5% requirement and can meet the inverter's requirements for DC measurement.
Conclusion: According to the requirements and regulations for DC component of photovoltaic grid-connected power generation system, in addition to using pulse width modulation technology, when selecting the corresponding current sensor, in addition to considering parameters such as high measurement accuracy, small linear error, wide temperature range, etc. Drift (zero temperature drift and gain temperature drift) is a particularly important parameter to consider. For sensors with the same nominal accuracy, the smaller the temperature drift, the smaller the influence on the DC component measurement. Therefore, the use of a good temperature drift sensor can effectively suppress the amount of direct injection, improve measurement results.
Bitcoin mining equipment is mainly highly specialized ASIC mill , The maximum computing power of a single miner is 110T/s( Ant S19Pro mill ), The scale of computing power of the whole network is 120EH/s above . Ethereum's mining equipment is mainly graphics card mining machine , Professional ASIC Mining machines are very few , On the one hand, it is because of the of Ethereum mining algorithm [ resist ASIC sex " Improved R & D efficiency ASIC The threshold of the miner , So how much do you know about the mainstream Ethereum mining machine ?
Ethereum mining algorithm has higher requirements for memory , The purpose of this design limits ASIC The use of chips in Ethereum mining . From the results , Most Ethereum mining machines are graphics card machines , This reflects the application of Ethereum mining algorithm ASIC Success on . From the absolute value of computational power scale , The computing power of Ethereum is about 200TH/s, The computing power of bitcoin is about 120EH/s, The latter is close to the former 60 ten thousandfold .
ASIC Mining machines have high computing power , Large power consumption , Like the latest ant S19Pro mill , Rated power consumption is 3250W, Need to consume... Every day 78 Degree electricity , According to the current currency price and 0.23 The electricity price in wet season is RMB , The proportion of electricity charge is 30.68%. Other older bitcoins ASIC mill , Like ants T17 series , The proportion of electricity charges generally exceeds 50%. by comparison , The power consumption of the graphics card miner is low , The proportion of electricity is also low . such as 5600XT8 Graphics card miner of card .
Ant S19-95T It adopts aluminum alloy profile electromechanical integrated design , Parallel four fan structure . According to the measured data , In line with and better than the official data .S19 The series is provided by TSMC 7nm chip , A new generation of customized chips with perfect whole machine architecture and high conversion rate APW12 Power Supply , Reduce power loss during conversion , Use more energy-saving , Greatly shorten the return cycle of the miner . In addition, the newly upgraded mining machine operation interface is also more humanized , Real time computing power . The average computing power and the operation of each chip are clear at a glance .
Shenma mining machine M30S-86T/88T/90T, Bit micro 2020 Launched in 2013 M30S Series of new mining machines , Announced that it would M30S The series is expanded to three 3X product . stay 3X In the new standard , Bit micro promises a one-year warranty for its series of products . This series of mining machines are provided by Samsung 8nm chip , Among them, god horse M30S series , The power consumption is 38J/T, Provide higher computing power , Lower power consumption and high stability.
Ethereum Mining Machine:Jasminer X4,Bitmain Antminer E9 (2.4Gh),iPollo V1,Jasminer X4-1U,iPollo V1 Classic,
Jasminer X4-C 1U,iPollo V1 Mini SE Plus
Ethereum Mining Machine,ETHW Miner,innosilicon a10 pro,E9 Antminer,Innosilicon A11
Shenzhen YLHM Technology Co., Ltd. , https://www.hkcryptominer.com